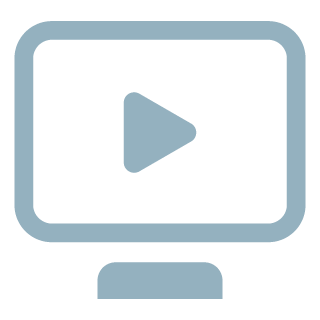
Simulation
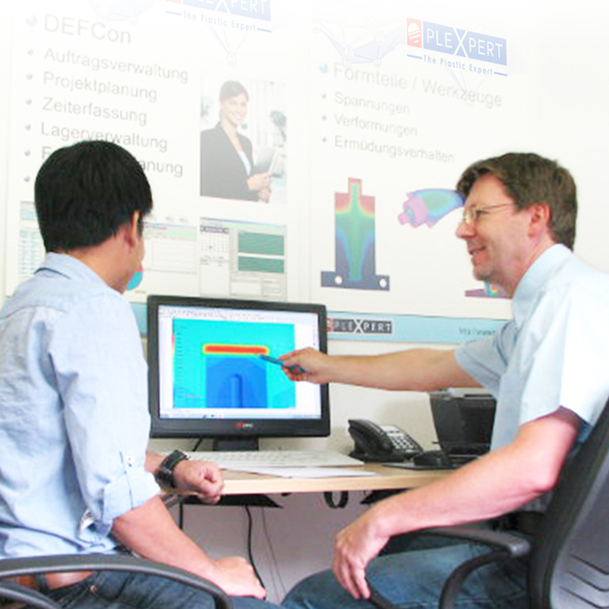

Designberatung
Anhand der Daten erstellen unsere Ingenieure eine Machbarkeitsanalyse unter Berücksichtigung des gesamten Folgeprozesses.
Sie profitieren vom Urteilsvermögen, der Kompetenz und langjährigen praktischen Erfahrung unseres Teams.
Dadurch erhalten Sie wertvolle Informationen zur weiteren Konstruktion des Formteils ohne kostspielige Umwege.
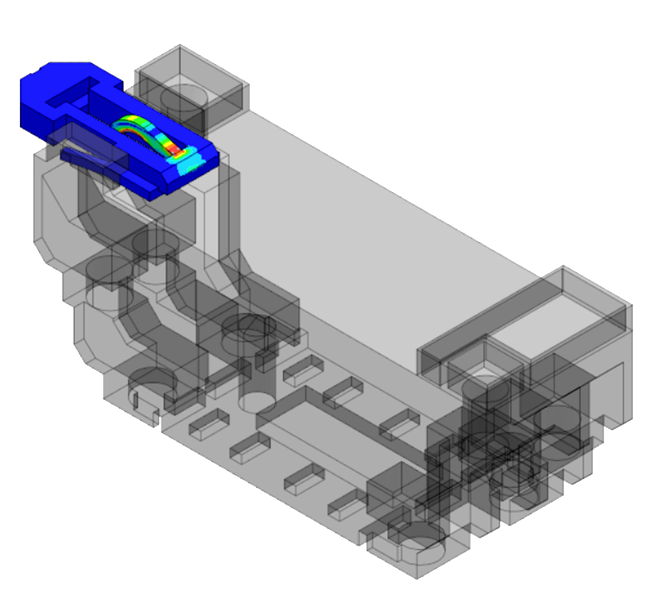
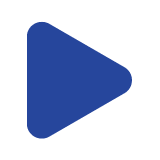
Strukturanalyse
Viele Formteil müssen im späteren Einsatz Kräfte aufnehmen.
In diesen Fällen ist es wichtig zu sehen, an welchen Stellen hohe Spannungen auftreten und welche Verformungen sich ergeben.
Die Orientierung von Glasfasern, sowie die Lage von Bindenähten spielen eine besondere Rolle und können unter Umständen problematisch werden.
Daher ist es unbedingt erforderlich, parallel zur rheologischen Berechnung eine Strukturanalyse durchzuführen.
Kritische Stellen werden erkannt und lassen sich durch rechtzeitig durch geeignete Maßnahmen optimieren.
Im Spritzgießprozess wirken Kräfte auf das Werkzeug.
Diese können insbesondere im Bereich von Kernen und Schiebern zu Problemen führen.
Durch Verformungen ändern sich z.B. Wandstärken am Formteil oder bei zu hohen Kräfte versagen Verriegelungen an Schiebern.
Die Strukturanalyse parallel zur Werkzeugkonstruktion bringt in der Entwicklung Sicherheit.
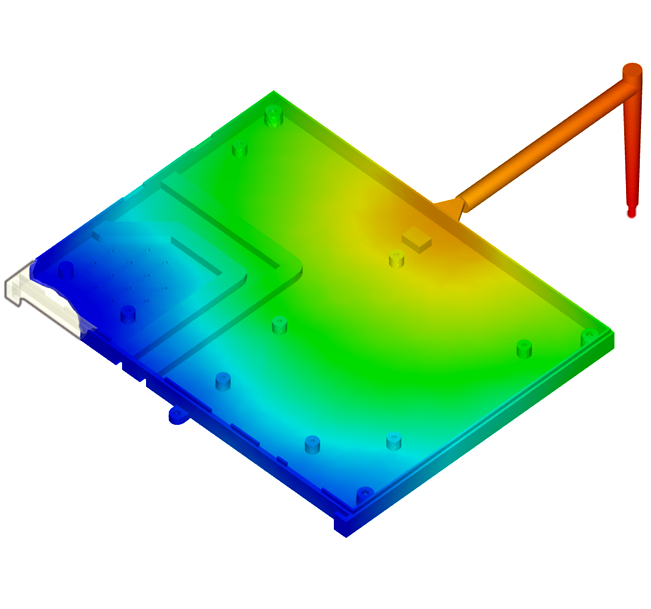
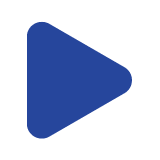
Formfüllung
Gängige Praxis muss sein, nach dem ersten Formteilentwuf eine Füllsimulation durchzuführen.
Die Lage der Anbindung und das Fließverhalten der Schmelze wird sichtbar.
Der Formteilkonstrukteur erkennt zum Beispiel wo Bindenähte entstehen werden.
Wandstärken an Formteilen lassen sich verringern um, das Gewicht des Teiles sowie die benötigte Produktionszeit zu reduzieren.
Durch die Simulation der Formfüllung lassen sich bereits 60% aller kritischen Punkte prüfen und beseitigen.
Dies ist der erste Schritt eine gute Formteilqualität sicherzustellen.
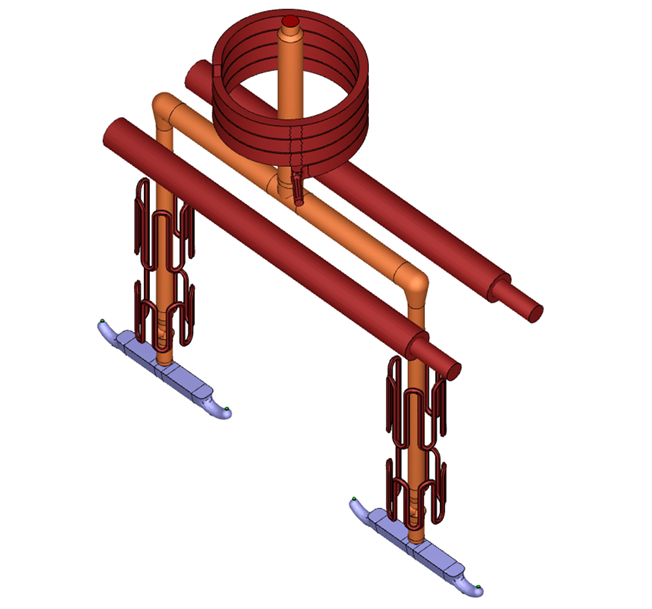
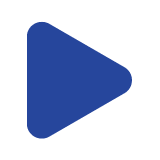
Verteilersystem
Nachdem das Formteil geometrisch beschrieben ist, wird die zukünftige Lage der Anbindung und das Verteilersystem definiert.
Hier befindet sich die Schnittstelle zwischen Formteil- und Werkzeugkonstruktion.
Es muss zum Beispiel festgelegt werden, ob ein Kaltkanal oder ein Heißkanalsystem zum Einsatz kommen soll.
Die Vor- und Nachteile der jeweiligen Systeme sowie der zu erwartende Druckverlust werden in der Simulation bestimmt.
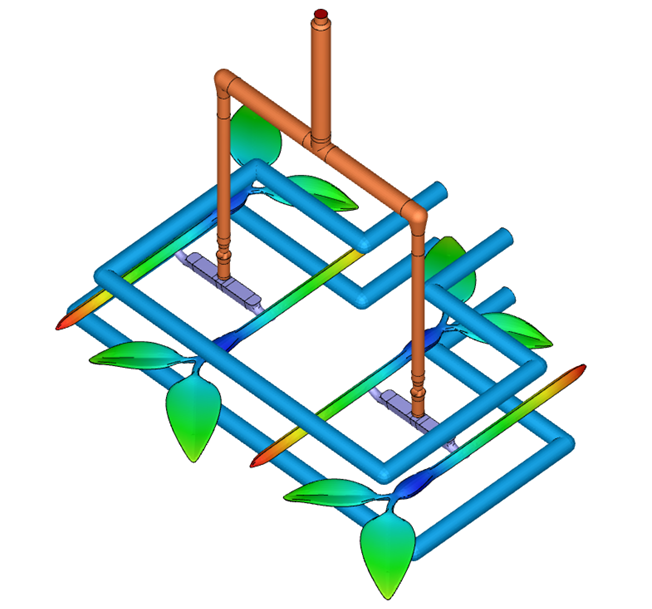
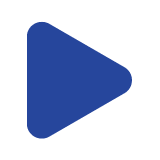
Werkzeugtemperierung
Während der Werkzeugkonstruktion wird das Temperiersystem festgelegt. Dabei wird eine homogene Werkzeugwandtemperatur angestrebt.
Durch die Simulation zeigt sich die Verteilung der Temperatur im Werkzeug und insbesondere am Formteil.
Hot Spots werden sichtbar und die Wirkung von Einsätzen mit unterschiedlichen Wärmeleitfähigkeiten deutlich.
Das Wichtigste ist jedoch die Ermittlung der schnellst möglichen Zykluszeit, denn diese hat wesentlichen Einfluss auf die zu erwartenden Stückkosten.
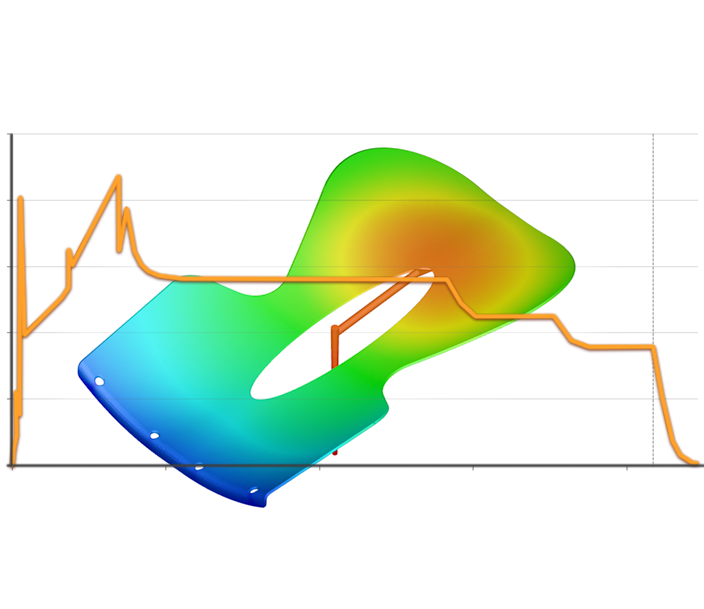
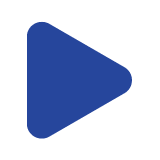
Nachdruckphase
Der Gewinn aus dieser Berechnung ist das Verständnis über das Erstarrungsverhalten am Formteil.
Darüber lässt sich erkennen, wo Einfallstellen oder Vakuolen entstehen können.
Bereiche mit hoher Schwindung, die zu Verzug führen können, werden erkannt und lassen sich verbessern.
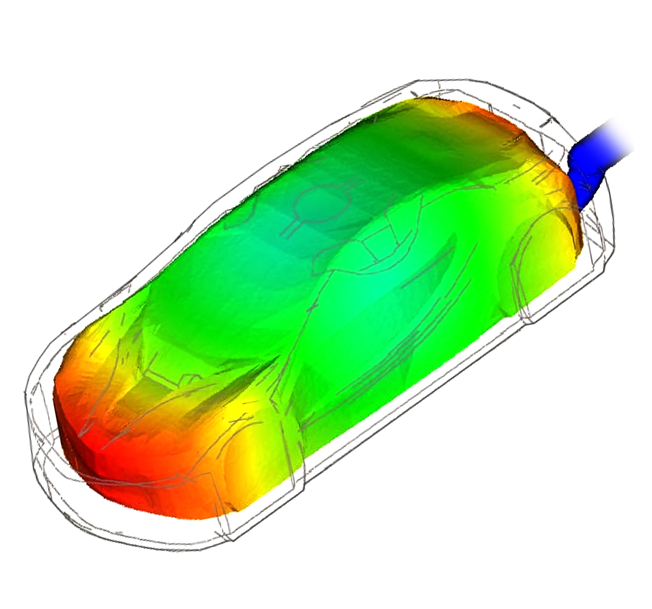
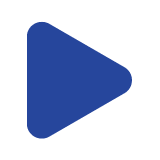
Verzug
Unbestritten ist der Verzug von Formteilen eines der größten Probleme bei der Herstellung von Kunststoffteilen.
Verschiedene Ursachen können dabei zur Deformation des Teiles führen.
Durch eine Simulation lassen sich die Ursachen bewerten und Maßnahmen festlegen, um den zu erwartenden Verzug zu minimieren.
Die Verzugsanalyse wird daher parallel zur Formteil- und Werkzeugkonstruktion durchgeführt.
Denn in diesen Phasen des Gesamtprozesses ist ein großer Spielraum gegeben um dem Verzug entgegen zu wirken.
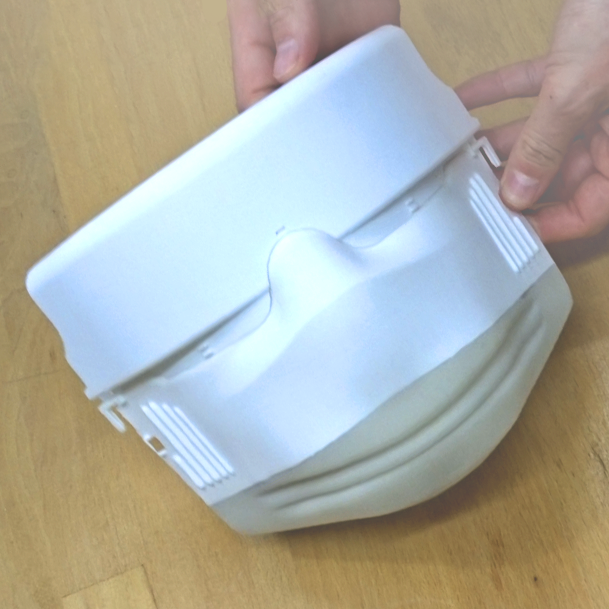

Prototyping
Dies ist der erste Schritt von der Simulation in Richtung Industrialisierung.
Gerne erstellen wir natürlich einen Prototyp für Sie auf der Basis von CAD Daten.
Doch wir gehen einen Schritt weiter und liefern Ihnen einen Prototyp auf der Basis der Simulationsergebnise.
Das Besondere dabei ist, dass wir damit den sich einstellenden Formteilverzug sowie die berechnete Materialschwindung im Prototyp wieder finden.
Diese Prototypen liefern wir auf der Basis von FDM, Photopolymer (Harz) oder im Vakuumguss auf PU Material.
Machen Sie den ersten Schritt in Richtung Fertigung.
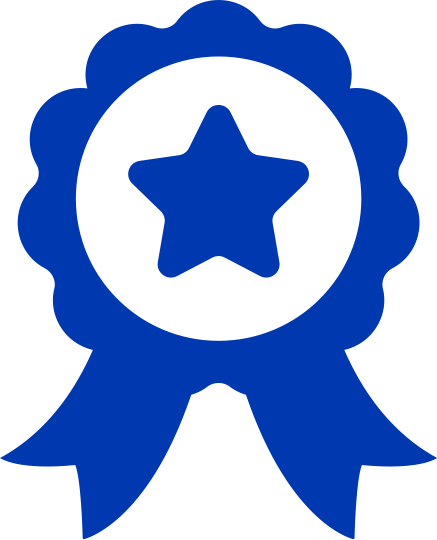
Eigene Berechnung oder Dienstleistung mit Expertise
Ob Sie eigene Berechnungen bei sich durchführen möchten, oder einen Dienstleister suchen.
Hier bei PLEXPERT sind Sie an der richtigen Adresse.
Als Vertriebspartner liefern wir die weltweit führende Simulationssoftware Moldex3D und unterstützten die Einführung und Anwendung bei Ihnen im Haus.
Gemeinsam finden wir das für Sie passende Paket von Modulen, damit Sie und Ihr Team schnell und effizient eigene Berechnungen machen können.
Als Dienstleister stellen wir Ihnen unser gesamtes KnowHow zur Verfügung, das in zahllosen Simulationsprojekten über die Jahrzehnte gewachsen ist.
Wir wissen worauf es ankommt und bewerten die Ergebnisse der Berechnung für Sie.
So profitieren Sie durch unsere Vorschläge für Optimierungen und nutzen unser umfassendes Prozessverständnis zu Ihrem Vorteil.
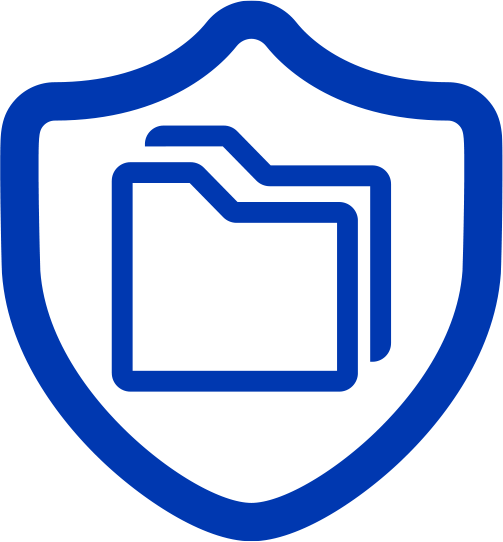
Dokumentation
Diese beinhalten natürlich die Analyse der Nachdruckphase unter Berücksichtigung des Verteilersystems.
Unabhängig von der Art der gewünschten Simulation werden alle relevanten Ergebnisse von uns beschrieben und gemeinsam besprochen.
Eine umfangreiche Dokumentation und detailierte Auswertung ist auf Wunsch möglich.
Diese wird parallel zu den Ergebnisdaten geliefert und beschreibt das Gesamtprojekt, wichtige Optimierungsstufen und das optimale Ergebnis aus den Simulationen.